The concept of modular homes has gained increasing popularity over the years due to their efficiency, cost-effectiveness, and environmental benefits. Unlike traditional stick-built homes, modular homes are pre-manufactured in sections, or modules, in a controlled factory environment and then transported to the building site for assembly modulinis namas.his innovative approach not only reduces construction time but also minimizes the environmental impact and provides homeowners with an affordable housing option without compromising quality or design.
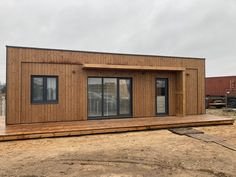
In this blog post, we’ll walk through the modular house building process, from design to assembly, so you can gain a deeper understanding of how these homes come to life.
1. Designing Your Modular Home
The journey of building a modular home begins with a clear and thoughtful design. Many modular home manufacturers offer a range of pre-designed floor plans to choose from, catering to various styles, sizes, and functionalities. However, custom designs are also available, allowing homeowners to personalize layouts and finishes according to their specific needs and preferences.
During the design phase, it’s important to consider:
- Layout: Decide on the number of bedrooms, bathrooms, and living spaces. You should also think about the flow of the spaces, considering factors like natural light, room sizes, and overall functionality.
- Style: Whether you prefer a traditional, contemporary, or modern design, there are countless architectural styles to choose from.
- Materials and Finishes: Modular homes offer flexibility in terms of finishes. Choose the materials for flooring, countertops, cabinetry, and siding based on your budget and style.
Once the design is finalized, the manufacturer will create blueprints and specifications to guide the production process.
2. Manufacturing the Modules
After the design is complete, the modular home enters the manufacturing phase. This is the stage where the modules are built in a factory setting. Building in a controlled environment has several advantages, including protection from weather-related delays, higher precision, and a consistent quality of work.
- Construction of Modules: The factory workers construct the individual modules, which typically consist of wall frames, floors, and roof sections. The modules are built with the same materials and techniques used in traditional home building, but they are assembled on a smaller scale.
- Incorporating Systems: During the manufacturing process, the home’s electrical, plumbing, and HVAC systems are installed into the modules. This means much of the work is done before the modules ever leave the factory, further reducing construction time.
- Quality Control: Every module is subject to thorough inspections and quality control checks to ensure that it meets the required standards. This is one of the key benefits of modular homes: the construction is often more consistent than that of site-built homes.
3. Transporting the Modules to the Site
Once the modules are completed and thoroughly checked, they are prepared for transportation. Each module is carefully loaded onto trucks and transported to the building site. The transportation process requires careful planning to ensure that the modules arrive at the site safely and in perfect condition.
In some cases, larger, more complex homes may have multiple trips and modules. However, most modular homes are delivered in 2-4 modules, depending on the size of the design.
4. Site Preparation and Foundation
While the modules are being manufactured, site preparation begins. This includes clearing the land, leveling the ground, and preparing the foundation. The type of foundation chosen (e.g., slab, crawl space, or full basement) will depend on local building codes, the landscape, and the type of modular home being built.
- Foundation Installation: A foundation is poured or constructed, typically using concrete. The foundation must be designed to bear the weight of the modules, and this step is essential for ensuring the structural integrity of the final home.
5. Assembly of the Modules
Once the modules have arrived at the site and the foundation is in place, it’s time for the assembly phase. This is where the modular home really starts to take shape.
- Lifting the Modules: Using cranes, the individual modules are carefully lifted and placed onto the foundation. Each module is connected to the others using steel connectors and bolts.
- Final Touches: Once the modules are in place, the construction crew connects the electrical, plumbing, and HVAC systems between modules. The roof is also fully constructed, and any exterior work, such as siding or roofing, is completed.
- Interior Finishes: Inside the home, workers complete any remaining touches, such as installing drywall, trim, flooring, and other finishes. Cabinets, countertops, and lighting fixtures are also added at this stage.
6. Final Inspections and Move-In
Before the home is ready for move-in, final inspections are conducted by both the manufacturer and local authorities. This ensures that everything is in compliance with local building codes and safety regulations.
Once the home passes all inspections, the utility connections (water, electricity, sewage, etc.) are finalized, and the home is officially ready for occupancy.
7. Advantages of Modular Homes
The modular building process offers several advantages over traditional home construction:
- Faster Construction Time: Since the modules are built in a factory and the foundation can be prepared concurrently, modular homes can be completed in a fraction of the time it would take to build a traditional home.
- Cost-Effectiveness: The controlled environment of the factory reduces waste, and bulk purchasing of materials can help lower costs, making modular homes an affordable choice for many homeowners.
- Quality Control: The factory setting allows for consistent quality checks, ensuring a high standard of craftsmanship.
- Environmentally Friendly: Modular homes typically generate less waste during construction, and the materials used are often more sustainable than traditional building materials.
Conclusion
The process of building a modular home, from design to assembly, is an efficient and sustainable alternative to traditional home construction. By embracing modern technology and factory-controlled environments, modular homes provide an affordable, high-quality, and customizable housing option. Whether you’re seeking a simple, cost-effective solution or a high-end, custom design, modular homes offer a variety of benefits that make them an excellent choice for many prospective homeowners.
4o mini